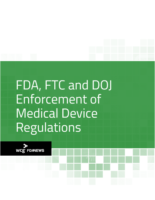
Home » Training Documentation: What Does the FDA Require?
Training Documentation: What Does the FDA Require?
Few things are more talked about in pharmaceutical manufacturing training than documentation and recordkeeping. Debates abound. Some issues training managers are grappling with include the following:
- What are the FDA’s documentation requirements?
- Does the organization need an electronic documentation system?
- Is validation of the electronic documentation system required?
- If validation is required, how is it done?
FDA does not specify training documentation requirements in its regulations, but investigators have made clear the importance of recordkeeping by the way they conduct inspections.
According to Phil Pontikos, Consumer Safety Officer with the FDA’s Columbus, Ohio, office, investigators evaluate employee competency through observation and interview rather than just document review.
But if investigators encounter areas of concern, they may turn to training documentation to "back into" an audit of a company's training program. This typically happens in one of three ways:
- Investigators ask to see an SOP and observe an employee perform the procedure. Depending on the employee's performance, they may ask to review the documents or records of the observed employee's training.
- Through investigation of production records, investigators spot deviations or out-of-specification issues. This in turn may lead to an examination of an operator's work and qualifications for the job. The investigators may ask how or what additional training was conducted and request the records that prove training was provided.
- Investigators identify processes or work practices that appear to be performed incorrectly during a routine tour of a manufacturing facility. They may ask to see the training materials or training records associated with individuals working in the area.
Many training managers have noted that if the training department can produce documentation quickly and in an organized fashion, FDA investigators are more likely to view the overall training effort as effective. At the same time, when solid training documentation cannot be produced quickly, a more in-depth review of the training system may occur.
Electronic Documentation Systems
Three methods are commonly used for training documentation/recordkeeping in the pharmaceutical manufacturing industry: paper systems, electronic systems with paper backup, and stand-alone electronic systems.
Some pharmaceutical companies use a paper-based documentation system, but most companies use some type of electronic system, with or without paper backup. These electronic systems, also known as Learning Management Systems (LMS), range from elaborate commercial programs to “home grown” databases created in Microsoft Access. Paper backup typically includes at least sign-in sheets and sometimes evaluation instruments.
An LMS is essentially a database made up of multiple tables to store discrete units of information. These might include employee information, course information, evaluation data, and training programs or materials. These tables can be merged and queried to produce specific reports. Report capabilities allow users to compare, analyze, question and project training needs.
Validating Electronic Documentation Systems
Pharmaceutical manufacturing training managers will debate about whether electronic training documentation systems need to be validated. To date, the FDA has not consistently required them to be validated, but manufacturers should do so to ensure the reliability of their performance.
Validation protocols should include repetitive testing to achieve a high degree of confidence that the results will be replicable. Systems should be validated under normal conditions as well as anticipated upset conditions. Finally, backup and recovery procedures must be developed and validated.
Once a system is validated and put into use, change control is necessary to maintain the validated state. All changes must be reviewed and approved prior to implementation. It is also a good idea to perform periodic reviews of the computer system. This involves a review of all changes over time as well as any problems that have occurred with the system.
Next week, we’ll look at the process of selecting, evaluating and implementing an electronic training documentation system.
Contact Information:
Dave Gallup
GMPTraining.com, Inc.
18585 Coastal Highway
Unit 10, #149
Rehoboth, DE 19971
215-870-5665
dagallup@gmptraining.com
www.gmptraining.com
Upcoming Events
-
07May
-
14May
-
30May