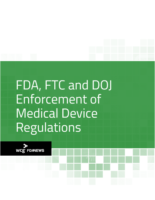
Home » FDA Strengthens Guidance on Quality Agreements with CMOs
FDA Strengthens Guidance on Quality Agreements with CMOs
Three years after issuing proposed guidance that laid out the FDA’s expectations for quality agreements with contract manufacturers, the agency has firmed up and expanded what drug companies must do to ensure that their agreements with CMOS are clear and enforceable.
In a final guidance issued yesterday, the FDA expanded the elements that should be included in most quality agreements. Specifically, the FDA says these agreements should include:
- The purpose/scope, which would explain the contract manufacturing services to be provided;
- Definitions, which would provide the precise meaning of terms in the quality agreement;
- Resolution of disagreements, which would explain how the parties will resolve disagreements about product quality issues or other problems; and
- Manufacturing activities, which would document quality unit and other activities related to manufacturing processes and the control of changes; and
- The life cycle of and revisions to the quality agreement.
Additionally, the FDA directs drugmakers to three ICH guidelines that contain recommendations on GMP: the Q7 Good Manufacturing Practice Guidance for Active Pharmaceutical Ingredients, Q9 Quality Risk Management and the Q10 Pharmaceutical Quality System.
The FDA also laid out specifications for materials management, including which party physically controls materials at all points in the manufacturing process, including the proper storage, transportation and shipping of materials.
In addition, the FDA states that the quality agreement should indicate which party will establish specifications for components as well as which party will establish processes for auditing, qualifying and monitoring component suppliers. The agreement should also identify which party will conduct required sampling and testing in compliance with CGMP.
FDA also recommends that the product-specific considerations section of the quality agreement include the parties’ expectations of each other regarding:
- Product/component specifications;
- Defined manufacturing operations, including batch numbering processes;
- Responsibilities for expiration/retest dating, storage and shipment, and lot disposition;
- Responsibilities for process validation, including design, qualification, and ongoing verification and monitoring; and
- Provisions to allow owner personnel access to the contract facility when appropriate.
Furthermore, the FDA says that in the quality agreement both parties should reach an agreement on how to address change control issues. Some of the expectations for reporting and approving changes that the quality agreement should address include: components and/or their suppliers, establishment locations, manufacturing processes, testing procedures, major manufacturing equipment and container closure systems.
Finally, the final guidance includes five case studies outlining different scenarios on facilities and equipment maintenance and upkeep at the contract facility; documenting steps in the manufacturing process; unreliable data in laboratory records and test results; contracted analytical testing laboratory and method validation; and approving or rejecting changes that affect product quality and CGMP compliance.
Few things in drugmaking are as challenging as process validation — nor as likely to trip you up with FDA inspectors. The most common mistakes occur after the work of validation has taken place: when documenting the work to show that it's been done. Order Managing Process Validation: A Drugmaker's Guide and gain the confidence to conduct process validations that reduce risk and satisfy regulators.
Upcoming Events
-
07May
-
14May
-
30May